UNIBLIMP EXPLAINED
UniBlimp idea, development and reality
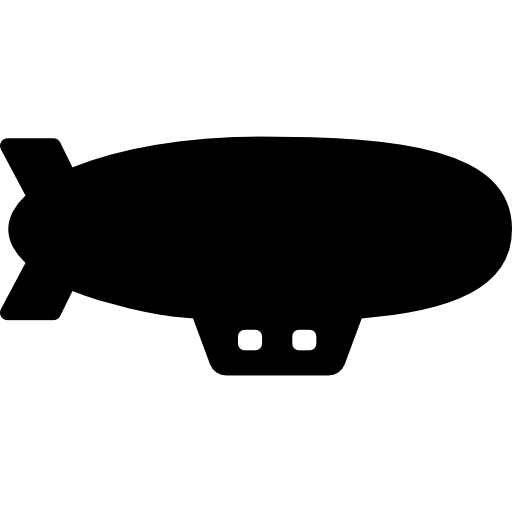

Aero Tunnel
As you can see clearly, on this wind tunnel simulation, the main resistance point is at the tip (nose) of the Blimp. That problem is solved by placing motor exactly on that location. By doing that we have not only eliminated the main resistance area but created a high pressure front that is actually “sucking” the air and eliminating the “nose” resistance. In the same time, the added bonus, the speed of the air flowing over the envelope, is accelerated creating a sort of “wind tunnel” that is covering the whole envelope. This “tunnel” effect is especially enhanced in our UniBlimp-Duo (front and back motor) where the front motor is “sucking” the air, directing it over the envelope and the back motor “sucking” it again reducing the time needed for the air to flow, therefore, reducing drag. With this “blimp tunnel effect", as we named it, the effect of cross and side winds is reduced up to 40% what is directly affecting less battery drain. The other direction was a logical deduction from the single motor concept. Stabilizers with ailerons reverse low stabilizer reverse motor and mount for the batteries and electronics where all that we needed to have a maneuverable and precisely controllable Blimp or Airship. All unnecessary weight was stripped to back up the main concept. RC BLIMP OR AIRSHIP ENVELOPE Everything is important with Blimps and Airships. But the envelope is obviously the main characteristic of a RC Blimps and Airships – “Big balloons that flies”. As main component of our UniBlimp we take exceptional care while designing and manufacturing envelopes. The process is: - 3D design of the envelope - Large format pattern print - Careful transfer of the 2D pattern on Polyurethane film (maximum 0.5% error) - Assembly on especially made tools - Double welding or triple welding technology process (depending on size) - After first inflation – rigorous quality control Respecting those production steps is paramount to produce a High Quality envelope that have maximum 0.5 to 1% of helium or hydrogen permeability on any volume per day. Stabilizers with ailerons are made of lightweight composite components resulting in large area super lightweight and strong control surfaces. We use High Quality imported UK Polyurethane which has been tested and retested over 20 years primarily by us (in all weather conditions) and ultimately by our clients.


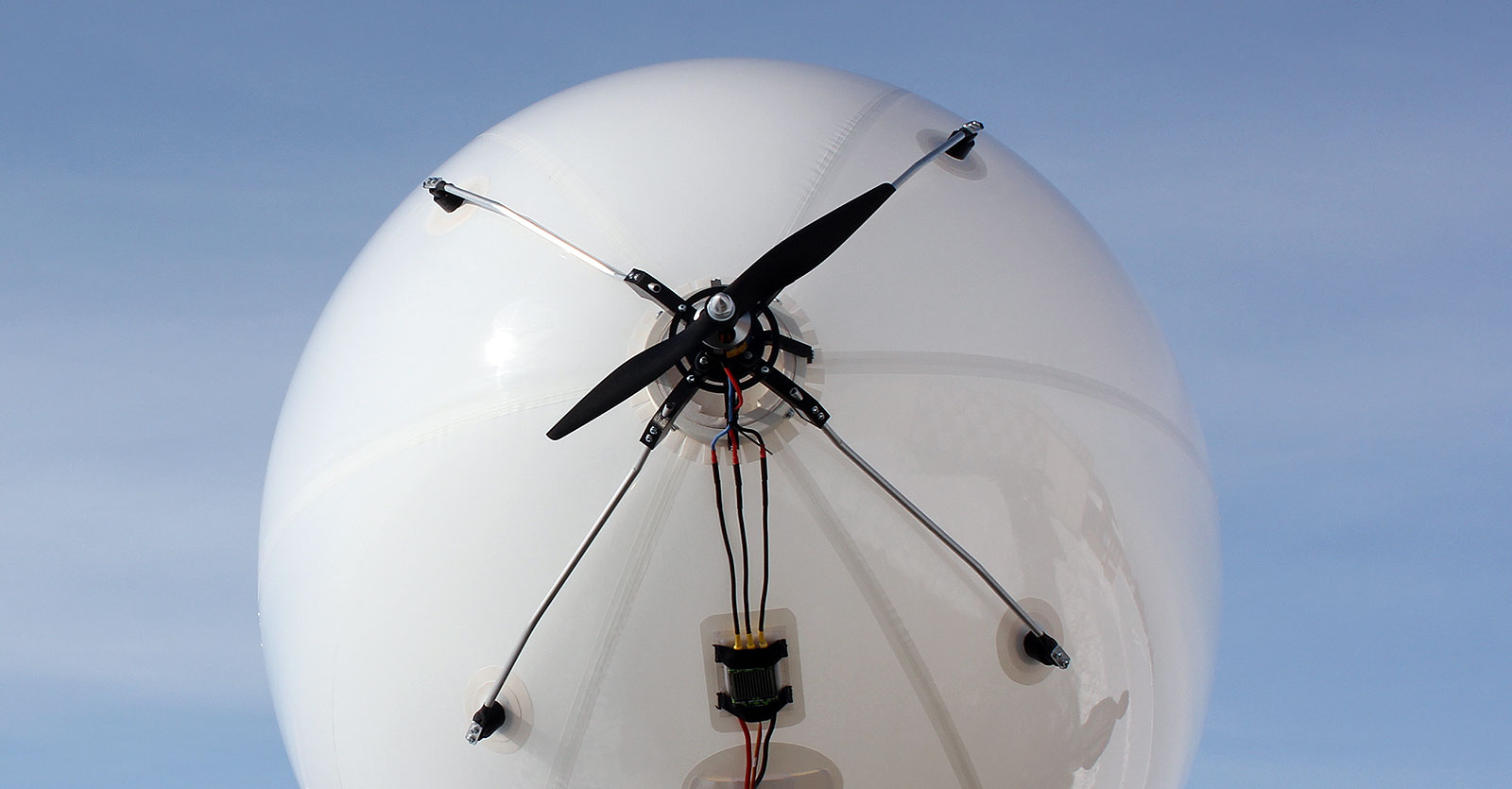
Reduced energy consumption
Thanks to the previous work on the T-Blimp, the results showed us that placing the main engine in the horizontal axis of the blimp has the best energy transfer with the least losses
Higher maneuverability
Since the resulting design is the largest possible distance between the drive motor and the control surfaces, the minimum displacement of the aileron strongly deflects the UniBlimp in 3D space
Longer autonomy
As a result of all the radical changes (relocating the engine to the nose, large distance between the engine and the stabilizer, and a radical reduction of the necessary electronics and components,...) we got a far greater flight autonomy than with the classic Blimp design.